The Mighty Zetros just got bigger Biglorryblog has the details on this custom build
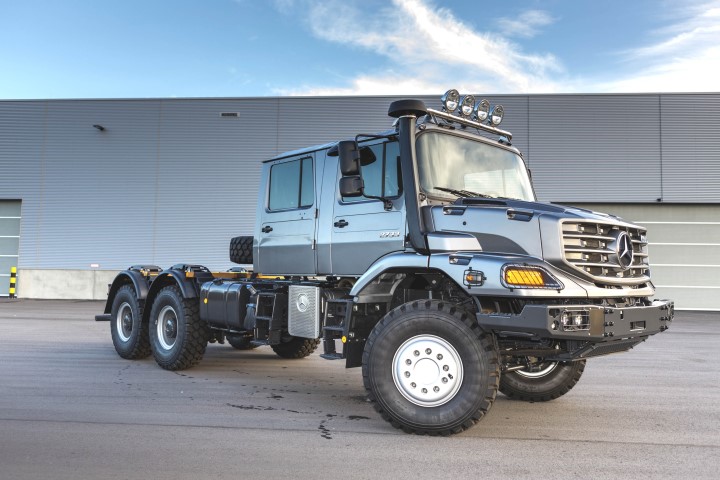
A Crew cab for the transport of working crews in the Mercedes-Benz Zetros A cab-over-engine truck is presented as 6×6 three-axle vehicle. It shows how a heavy-duty truck for extremely harsh off-road crew transports in applications such as mining and open-cast mining has to be built. Equipped with a crew cab, it is an outstanding example for the efficient co-operation between Mercedes-Benz Special Trucks (MBS) at Wörth in Germany, the Mercedes-Benz manufacture Custom Tailored Trucks (CTT) at Molsheim in France and their qualified partner Paul Nutzfahrzeuge at Vilshofen, which is also located in Germany.
Paul Nutzfahrzeuge has extended the driver’s cab by 700 mm and expanded it to become a fully-fledged crew cab for safe staff transports of up to six crew members. The underbody was converted by additionally welded longitudinal beams and cross members, the roof area by inserting additional frame sections and cross bows. Furthermore, the Paul engineers moved the rear panel including the original trim of the Zetros to the rear by 700 mm altogether.
For the installation of the crew cab it became necessary to reposition the air dryer and the air valves on the left side of the vehicle to the rear end. The side panels and the doors including windows, interior trim etc. are taken from the crew cab of the Unimog U 5000 and were adapted accordingly.
On the rear bench seat with head restraints, coat hooks and three-point seat belts up to four crew members of the operational team can be seated in direction of travel. Three separate treads on the left as well as on the right side of the cab facilitate their rapid entry and exit. They are almost identical with the original Zetros treads for driver and front passenger in the front part of the cab and their mounting was also adapted accordingly by Paul Nutzfahrzeuge. After conversion the interior is equipped with a high-performance air conditioning system with two outlets which ensure comfortable temperatures for the crew on board even with high outside temperatures.
Strong five-axle carrier chassis for Cifa concrete pump
Paul Nutzfahrzeuge configures special five-axle carrier chassis for the self-propelled Carbotech truck-mounted concrete pumps of the type K60H which are produced by the concrete machine manufacturer Cifa S.p.A. from Senago near Milan, Italy. The installation of a steered and air-suspended trailing lift axle at the rear with a load capacity of 12 t is a characteristic feature. The installation on the exhibition vehicle at the Bauma 2016 is based upon a Euro-6 chassis of the Mercedes-Benz Arocs range delivering an output of 375 kW/510 hp. The modified five-axle chassis bears the type designation Arocs 5551 K 10×4/6 and offers an increased load capacity of 42 t at a maximum gross vehicle weight of 55 tons. The conversion measures optimize the distribution of weight on the individual axles when transporting the concrete pump which is fixed and firmly mounted on the frame of the chassis.
The electro-hydraulic steering system increases the maneuverability of the vehicle combination on narrow construction site areas so that the turning circle of the five-axle truck of 25 m does not exceed the radius of the Arocs standard chassis. Thus, pumping processes in extreme heights can be carried out even in cramped conditions – in the process, the lift mechanism of the rear axle automatically activates as soon as the signal to extend the support stands is sent.
The air suspension of the steered axle allows a particularly material-preserving transport of the heavy construction equipment to the site of operation. Apart from the load relief of the other axles it is at the same time a relevant precondition for the implementation of the starting assistance which is operative up to 30 km/h and which is also installed into the vehicle by Paul Nutzfahrzeuge.
The fact that the original wheelbase could be maintained to adhere to the overall length of the chassis (10.75 m) and of the complete vehicle (13.4 m), as well as the possibility to make use of the short CompactSpace-M driver cab from series production helps to keep the cost low. To allow this and at the same time adhere to the predetermined overall height of the vehicle of less than four meters the frame height was reduced to 1,060 mm. Furthermore, the frame overhang at the rear end was reduced to 2,450 mm, the end crossmember was removed and the second front axle is repositioned by 300 mm to the rear in combination with the adaptation of the spring and axle connection.